In Nederland werken veel mensen met passie met biomassa als grondstof. Ze werken aan innovaties, verbeteren (productie)processen of maken beleid voor een fossielvrije toekomst. We hebben een reeks gesprekken gevoerd met mensen die werken bij bedrijven waar biogrondstoffen centraal staan. Wij belichten in deze miniserie wat hun drijfveren zijn om te werken aan de transitie naar een duurzame wereld. In de zesde aflevering hebben wij een gesprek met Alexander Hooijmaaijers van Martens keramiek.
Het ontwikkelen van duurzaam vastgoed wint steeds meer terrein, want met duurzaam bouwen valt snel en doeltreffend winst te behalen. In ecologisch en maatschappelijk, maar ook in economisch opzicht. Toch komt de bouwsector slechts aarzelend op gang.
In een tijd waarin de roep om milieubewustzijn en duurzaamheid steeds luider klinkt, speelt de bouwsector een cruciale rol in het realiseren van positieve veranderingen. Duurzaam bouwen gaat verder dan alleen het verminderen van de ecologische impact. Het omvat ook sociale verantwoordelijkheid en economische voordelen, waardoor het een integrale benadering is voor het creëren van vastgoed dat niet alleen de huidige behoeften vervult, maar ook rekening houdt met toekomstige generaties.
Wij spraken met Alexander Hooijmaaijers, teamleider verkoop bij Martens keramiek. Martens produceert kunststof, beton en keramische bouwmaterialen. Martens is voornamelijk bekend met de weg- en waterbouw. Met een nieuwe productlijn introduceerden ze zichzelf in de bouwbranche. In 2018 is Martens keramiek opgericht. Onder de merknaam Kerloc produceren ze biobased keramische gevelbekleding. De gevelbekleding is 100% circulair en heeft een lange levensduur.
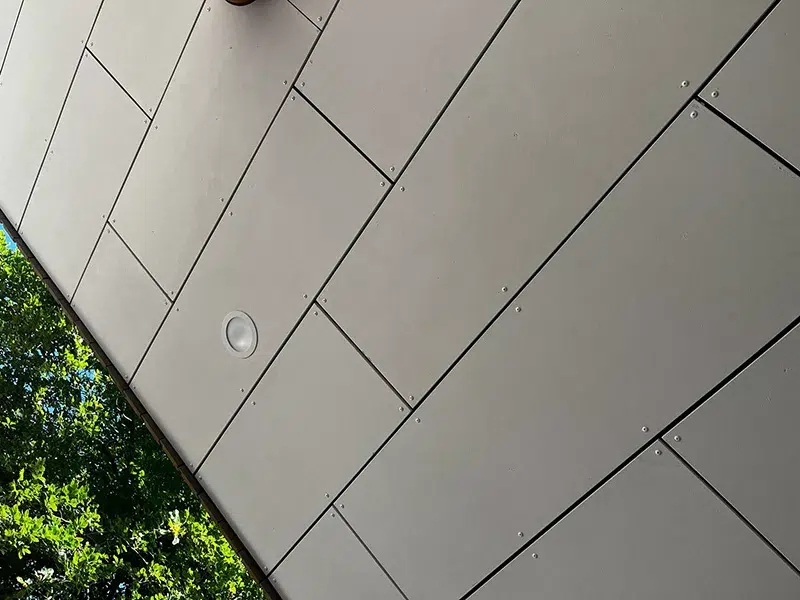
Alexander Hooijmaaijers: “In mijn vorige werk heb ik veel gereisd. Ik werkte bij een Japanse fabrikant die over de hele wereld distribueerde. Door dit werk heb ik alle hoeken van Europa gezien, elke maand een week in Japan en daardoor nooit lang in Nederland. Ik heb ontzettend veel met het vliegtuig gereisd. Zo’n 5-6 jaar geleden kreeg ik de bewustwording dat dit een negatieve impact op het milieu heeft. Dat zette me aan het denken. Waar was ik mee bezig? Hoe zie ik de toekomst van mijn kinderen? Bij veel mensen begint nu de urgentie in te dalen dat we iets moeten doen voor het klimaat en milieu. Ik ging op zoek naar een andere baan, want ik voelde mij niet meer thuis in deze manier van werken. Ruim vijf jaar geleden ben ik gevraagd door Martens of ik interesse had om bij hun te gaan werken om een nieuwe productlijn op te starten. Binnen Martens is duurzaamheid al jaren een belangrijk thema en de rode draad binnen de productieafdelingen. Martens had als doel gesteld om een geheel nieuw, duurzaam en 100% circulair product te ontwikkelen. Van een idee komen tot een daadwerkelijk product en dat ook nog eens duurzaam, circulair en biobased is, dat sprak mij enorm aan. We maken hiermee wel een statement naar alle traditionele fabrikanten. Dat dit de manier gaat worden hoe men omgaat in de bouw, dat het kan en eigenlijk ook moet.”
Het proces van hout naar keramiek plaatmateriaal is niet vanzelf gegaan. Door een overname van een productielijn kwam Martens in aanraking met plaatmateriaal. Die productielijn probeerde van afval van aubergines plaatmateriaal te maken.
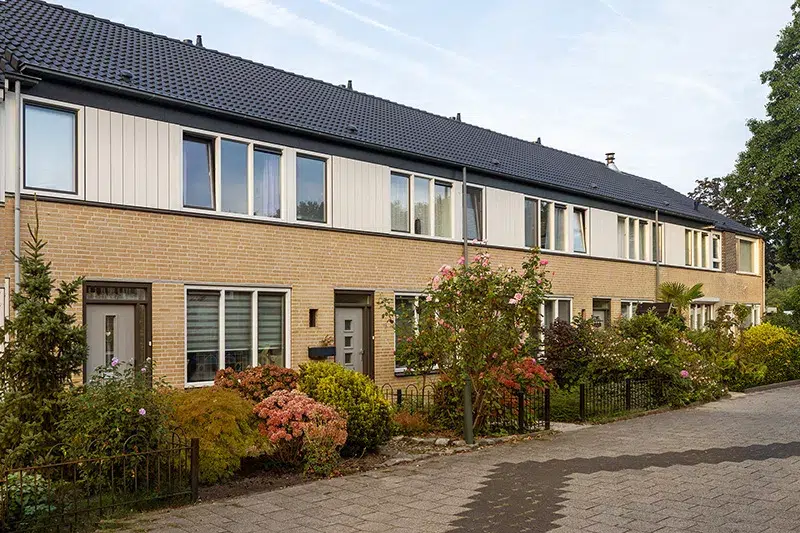
Alexander: “Het ontwikkelteam van Martens vond het idee van de productielijn die ze overnamen helemaal zo gek nog niet. Een collega van ons ontwikkelteam heeft 20-25 jaar geleden al gezegd dat hout kan verstenen in de natuur. Hout wat onder de grond ligt versteend. Grondwater dat langzaam door de bodem sijpelt, zet mineralen af op plaatsen waar lignine en cellulose wegrotten. Dit proces kun je proberen scheikundig na te bootsen. Onze collega was er van overtuigd dat dit kon. Hij ging aan de slag met potjes en pannetjes en met wat ingrediënten en na een paar maanden kwam hij hiermee terug. Er moest nog wat aan geschaafd worden, maar hij dacht het haalbaar was. In 1,5 tot 2 jaar hebben we het ontwikkeld. Met het team dachten we als we zoiets kunnen produceren, waar kunnen we impact maken? Waar is de marktbehoefte zo groot dat je daar een positieve impact mee kunt maken? Je kan het super romantisch maken, maar we moeten ook een rendabele businesscase hebben, dus waar heb je afzet nodig? We hebben diverse rapporten doorgenomen. In één van die rapporten blijkt dat er jaarlijks 123 miljoen m2 gevelbekleding nodig is. Dat is op zich niet zo heel veel, maar als je in gaat zoomen, dan ligt het leeuwendeel van die behoefte in Europa. Hiermee kunnen we een impact maken en hebben we een rendabele businesscase. Dus zodoende is eigenlijk de toepassing en de markt bepaalt.
Uiteindelijk is ons doel om ons product volledig uit reststromen te laten bestaan. We gebruiken populierenhout. Dat zijn gewoon Nederlandse Populieren die hier gesnoeid of gerooid worden. Van het hout maken we draadvezels. En die draadvezels gaan wij verharden. Hout is hout zou je denken, maar dat is niet zo.
Op een gegeven moment hadden we het juiste recept gevonden. Wat we konden herhalen qua schaalvergroting, want eerst ga je kleine plaatjes maken en dan ga je kijken, hoe gedraagt het zich, wat doet het, kun je het gaan herhalen. Nadat een batch op was en een nieuwe werd gebruikt bleek dat de sterkte van het materiaal niet hetzelfde was. Wat bleek, al het hout die wij al die tijd getest hadden waren populieren gerooid in het najaar en de nieuwe batch was gerooid in het voorjaar.
Zo leer je dat er allemaal parameters ineens veranderen in zo’n proces. Omdat we het populierenhout nu zo goed kennen kunnen we, om de kwaliteit te waarborgen, niet zomaar overstappen op een andere houtsoort of een ander bio-materiaal.
Bij echt keramiek bak je klei in de oven op 1200 graden, dan verhard het product. Dat kan bij hout natuurlijk niet. Ons proces om Kerloc te maken is wel eenzelfde soort proces. Wij gebruiken mineralen om de houtdraden te verharden. Houtvezels zijn flexibel. Dat maken we door een scheikundige werking van mineralen hard. Mineralen worden gedolven om het te krijgen, dus daar wil je uiteindelijk vanaf. Dat heeft een impact op ons product, maar voor nu hebben we het nog nodig. We blijven ons ontwikkelen zodat we hopelijk ook dat proces volledig op een duurzame manier kunnen gebruiken.”
Onbekend maakt onbemind, is ook van toepassing op de bouw. De bouw is traditioneel. Een architect wil iedere keer iets nieuws of iets unieks ontwikkelen. Dat is een beetje de signature qua vormgeving, maar ga je kijken naar de materialen dan zijn het bijna altijd dezelfde materialen die gebruikt worden.
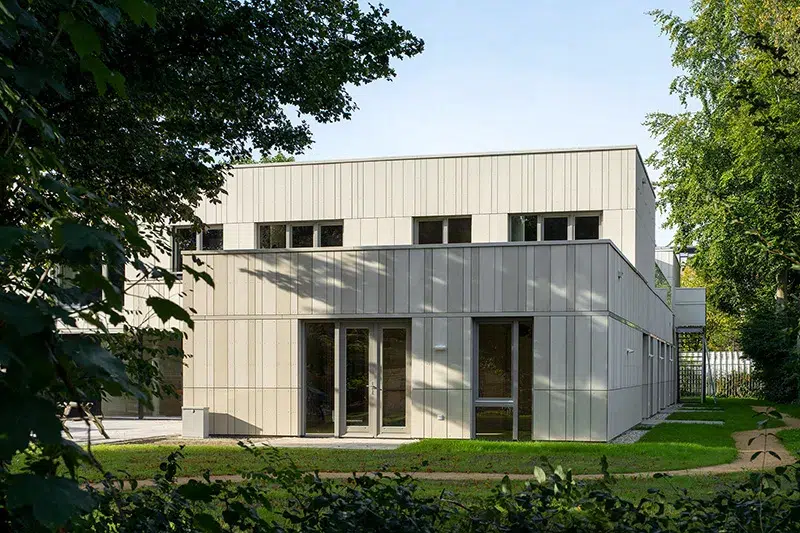
Alexander: “Wij hebben goede gesprekken met architecten, projectontwikkelaars, met overheden en ook met corporaties en gemeenten. Die zijn allemaal enthousiast. We merken wel dat de aannemer conservatiever is. Nieuwe producten kosten tijd om te leren hoe er mee om te gaan en om te begrijpen hoe het toegepast kan worden. Dit komt uiteindelijk wel goed. Het totale proces kost gewoon tijd.
Ik vind het persoonlijk mooi om in dat hele proces een bijdrage te kunnen leveren. Dat ik, als persoon, en als bedrijf bij kan dragen dat de bouw duurzamer en bewuster wordt.”
Wat maakt Kerloc 100% circulair?
Door het duurzame karakter (50+ jaar) gaat het langer mee dan een technische of economische levensduur van een object, waardoor het geschikt is voor demontage en her te gebruiken middels remontage.
De gebruikte platen kunnen teruggenomen worden en (volledig en oneindig binnen eigen productieproces) hergebruikt worden bij de productie van nieuwe Kerloc gevelbekleding.
Restafval bij ons productieproces is geen afval, omdat ook het restafval hergebruikt wordt bij de productie van nieuwe Kerloc gevelbekleding. In tegenstelling tot traditionele gevelbekleding maakt dit Kerloc tot een volwaardig circulair alternatief.